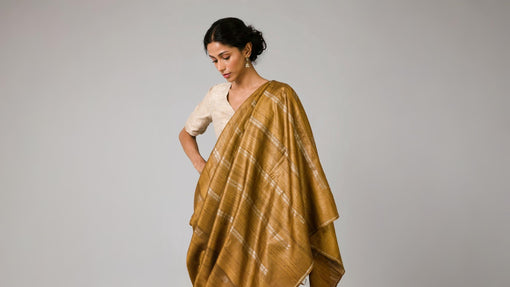
Once upon a time, there lived a demon named Maisasur. He was believed to be so powerful that an army of Gods were unable to stop him. Finally came Goddess Durga, who defeated the power-hungry demon after 10 days of vicious battle. To thank her, the local tribes, particularly the Dewangan community created a unique type of Silk Saree just for her.
Thus Kosa silk originated.
These Kosa silk sarees sure have folklore and mythology woven into them, but that is not the only thing that makes them special. They undergo an intricate silk manufacturing process, making them one of the most glamorous fabrics ever produced in India.
Let’s take a closer look at this process, shall we?
Join us as we take you through the tropical journey of this beautiful Indian silk sari fabric from silkworm to loom.
1. The Silkworms: Nature's Unseen Artisans
The story of Kosa silk takes off in the lushness of the Indian jungles of Chhattisgarh, home to the Antheraeamylitta silkworm. These are Indian wild silkworms that live in sal and arjun trees. Contrary to mulberry silkworms that are raised in strictly controlled environments, these silkworms live in the wild, feeding on the leaves of the forest making this an ecologically responsible beginning to the silk manufacturing process. Their method of feeding actively embraces and sustains biodiversity without putting any demand on the environment.
2. Cocoon Collection: Forest to Village
Once the silkworms have spun their cocoons and completed their metamorphosis life cycles, their cocoons are collected. Tribal communities, like the ones in Champa, Korba, and Raigarh, have been passing down this knowledge of harvesting silk for generations.
In traditional silk production, the pupa is generally boiled alive to produce longer fibers. When using Ahimsa (peace) silk or in other words non-violent Kosa, the moth is allowed to emerge. This produces shorter filament threads, however, it is more appropriate in terms of eco-fashion and ethical-values.
3. Boiling & Degumming: Washing the Silk
The raw cocoons are boiled, before or after the moth emerges to soften the sericin, a protein responsible for binding the cocoon together. This method is known as degumming, and serves to loosen and clean the silk fibers whilst keeping the silk strong.
It’s a vital part of the silk manufacturing process, one that requires precision and care to retain the fabric's signature durability and flexibility.
4. Reeling the Yarn: A Hand-Spun Custom
After boiling the silk, the silk fibres are processed through a hand-reeling process into threads. This process is done on a traditional spinning wheel or charkha, as the hand-reeling process is still preferred in rural areas. This is a slow time-consuming process. It creates inconsistency in texture, slight irregularity, etc.
Once the silk yarn has been spun, it is washed, dried under the sun, and graded as to quality by the luster, weight, and thickness.
5. Natural Dyeing: Color from the Earth
The most sustainable aspect of Kosa silk is the coloring process and its ability to absorb all-natural dyes. Many weavers still dye their yarns with plant-derived, mineral, or herbal ingredients. Yellows could come from turmeric, green from haritaki, and red from madder root.
Not only does this have a low environmental footprint but it also provides muted, earth-tone colors that appeal to sustainable fashion lovers and lovers of pure tussar silk sarees.
6. Weaving: Where Art and Soul Meet
Once the yarns are dyed and dried, they are ready for weaving. The artisans will weave with traditional pit looms or frame looms to make the silk fabric. Depending on the intricacy of the design and the width of the fabric, weaving a Kosa saree could take days to weeks.
The artistry of weaving results in beautiful items, stunningly elegant Kosa silk sarees - rich in texture, storytelling, and weaving mastery. Whether a simple drape or embellished or layered, each Kosa saree is a reflection of the time, patience, and skill of the artisan that made it.
7. Finishing Touches: Fabric to Fashion
After weaving, the sarees are washed, starched, and finished. Artisans may also hand-embroide the borders or pallu with local motifs and cultural symbols.
Today, Kosa silk sarees are worn not only on traditional occasions but as contemporary, sustainable fashion pieces. Kosa silk sarees do great double duty for occasion and dress code, as they can be stunning when paired with antique jewelry or combined with contemporary silhouettes, and can be worn year-round or for casual or formal settings, from weddings to work events.
Why This Process Matters
Everything that goes into Kosa silk, from the forest to the loom, represents sustainability, ethical practices, and cultural pride. This is important because it makes it:
-
Eco-Friendly: No industrial machines or chemical dyes
-
Ethically-Made: Provides support to tribal weavers and rural livelihoods
-
Culturally Rich: Each saree carries a story from the heart of India
-
Durability: Resistance to dust and fading, breathable and age-friendly
It’s not a saree, it’s a story
In a world that thrives on fast fashion, Kosa silk offers a shining positive example of conscious luxury — one that is not compromised by beauty, ethics, or tradition. Every strand of Kosa silk carries with it generations of wisdom, a respect for nature, and timeless craftsmanship — from cocoon to saree.
Next time you wear or admire plain tussar silk sarees, do remember: They are not just clothing. They are a part of our heritage - raw, real, and beautifully grounded in India's cultural soil.